Mikroskop elektron pengimbasan digunakan untuk memerhati patah keletihan dan menganalisis mekanisme patah; pada masa yang sama, ujian kelesuan lentur putaran telah dijalankan ke atas spesimen yang dinyahkarburkan pada suhu yang berbeza untuk membandingkan hayat kelesuan keluli ujian dengan dan tanpa penyahkarbonan, dan untuk menganalisis kesan penyahkarbonan ke atas prestasi keletihan keluli ujian. Keputusan menunjukkan bahawa, disebabkan kewujudan serentak pengoksidaan dan penyahkarbonan dalam proses pemanasan, interaksi antara kedua-duanya, mengakibatkan ketebalan lapisan dekarburisasi sepenuhnya dengan pertumbuhan suhu menunjukkan trend meningkat dan kemudian menurun, ketebalan lapisan dekarburisasi sepenuhnya mencapai nilai maksimum 120 μm pada 750 ℃, dan ketebalan lapisan dekarburasi sepenuhnya mencapai nilai minimum 20 μm pada 850 ℃, dan had keletihan keluli ujian adalah kira-kira 760 MPa, dan punca rekahan keletihan dalam keluli ujian adalah terutamanya kemasukan bukan logam Al2O3; tingkah laku penyahkarbonan sangat mengurangkan hayat keletihan keluli ujian, menjejaskan prestasi keletihan keluli ujian, semakin tebal lapisan penyahkarbonan, semakin rendah hayat keletihan. Untuk mengurangkan kesan lapisan penyahkarbonan pada prestasi keletihan keluli ujian, suhu rawatan haba optimum keluli ujian hendaklah ditetapkan pada 850 ℃.
Gear adalah komponen penting dalam kereta, disebabkan oleh operasi pada kelajuan tinggi, bahagian meshing permukaan gear mesti mempunyai kekuatan tinggi dan rintangan lelasan, dan akar gigi mesti mempunyai prestasi keletihan lentur yang baik disebabkan oleh beban berulang yang berterusan, untuk mengelakkan keretakan yang membawa kepada bahan patah tulang. Penyelidikan menunjukkan bahawa penyahkarbonan adalah faktor penting yang mempengaruhi prestasi keletihan lenturan putaran bahan logam, dan prestasi lenturan lenturan putaran merupakan penunjuk penting kualiti produk, jadi adalah perlu untuk mengkaji tingkah laku penyahkarbonan dan prestasi keletihan lentur putaran bahan ujian.
Dalam makalah ini, relau rawatan haba pada ujian penyahkarbonan permukaan keluli gear 20CrMnTi, menganalisis suhu pemanasan yang berbeza pada kedalaman lapisan penyahkarbonan keluli ujian perubahan undang-undang; menggunakan mesin ujian keletihan rasuk mudah QBWP-6000J pada ujian kelesuan lenturan putar keluli ujian, penentuan prestasi keletihan keluli ujian, dan pada masa yang sama untuk menganalisis kesan penyahkarburan pada prestasi keletihan keluli ujian untuk pengeluaran sebenar untuk meningkatkan proses pengeluaran, meningkatkan kualiti produk dan menyediakan rujukan yang munasabah. Prestasi keletihan keluli ujian ditentukan oleh mesin ujian keletihan lentur putaran.
1. Bahan dan kaedah ujian
Bahan ujian untuk unit untuk menyediakan keluli gear 20CrMnTi, komposisi kimia utama seperti yang ditunjukkan dalam Jadual 1. Ujian penyahkarbonan: bahan ujian diproses menjadi spesimen silinder Ф8 mm × 12 mm, permukaan harus cerah tanpa noda. Relau rawatan haba dipanaskan kepada 675 ℃, 700 ℃, 725 ℃, 750 ℃, 800 ℃, 850 ℃, 900 ℃, 950 ℃, 1,000 ℃, ke dalam spesimen dan tahan 1 jam, dan kemudian disejukkan ke suhu bilik. Selepas rawatan haba spesimen dengan menetapkan, mengisar dan menggilap, dengan 4% daripada hakisan larutan alkohol asid nitrik, penggunaan mikroskop metalurgi untuk memerhati lapisan penyahkarburan keluli ujian, mengukur kedalaman lapisan penyahkarbonan pada suhu yang berbeza. Ujian keletihan lenturan putaran: bahan ujian mengikut keperluan pemprosesan dua kumpulan spesimen keletihan lenturan putaran, kumpulan pertama tidak menjalankan ujian penyahkarbonan, kumpulan kedua ujian penyahkarbonan pada suhu yang berbeza. Menggunakan mesin ujian keletihan lentur putaran, dua kumpulan keluli ujian untuk ujian keletihan lentur putaran, penentuan had keletihan dua kumpulan keluli ujian, perbandingan hayat keletihan kedua-dua kumpulan keluli ujian, penggunaan pengimbasan pemerhatian patah keletihan mikroskop elektron, menganalisis sebab-sebab patah spesimen, untuk meneroka kesan penyahkarburan sifat keletihan keluli ujian.
Jadual 1 Komposisi kimia (pecahan jisim) keluli ujian wt%
Kesan suhu pemanasan pada penyahkarburan
Morfologi organisasi penyahkarbonan di bawah suhu pemanasan yang berbeza ditunjukkan dalam Rajah 1. Seperti yang dapat dilihat dari rajah, apabila suhu ialah 675 ℃, permukaan sampel tidak kelihatan lapisan penyahkarbonan; apabila suhu meningkat kepada 700 ℃, lapisan penyahkarbonan permukaan sampel mula muncul, untuk lapisan penyahkarburan ferit nipis; dengan suhu meningkat kepada 725 ℃, ketebalan lapisan penyahkarburan permukaan sampel meningkat dengan ketara; Ketebalan lapisan penyahkarbonan 750 ℃ mencapai nilai maksimumnya, pada masa ini, butiran ferit lebih jelas, kasar; apabila suhu meningkat kepada 800 ℃, ketebalan lapisan penyahkarbonan mula berkurangan dengan ketara, ketebalannya jatuh kepada separuh daripada 750 ℃; apabila suhu terus meningkat kepada 850 ℃ dan ketebalan penyahkarbonan ditunjukkan dalam Rajah 1. 800 ℃, ketebalan lapisan penyahkarbonan penuh mula berkurangan dengan ketara, ketebalannya jatuh kepada 750 ℃ apabila separuh; apabila suhu terus meningkat kepada 850 ℃ dan ke atas, keluli ujian ketebalan lapisan penyahkarbonan penuh terus berkurangan, separuh ketebalan lapisan penyahkarbonan mula meningkat secara beransur-ansur sehingga morfologi lapisan penyahkarbonan penuh semua hilang, separuh morfologi lapisan penyahkarbonan beransur-ansur jelas. Ia boleh dilihat bahawa ketebalan lapisan dekarburisasi sepenuhnya dengan peningkatan suhu mula-mula dinaikkan dan kemudian dikurangkan, sebab fenomena ini adalah disebabkan oleh sampel dalam proses pemanasan pada masa yang sama tingkah laku pengoksidaan dan penyahkarbonan, hanya apabila kadar penyahkarburan lebih cepat daripada kelajuan pengoksidaan akan muncul fenomena penyahkarbonan. Pada permulaan pemanasan, ketebalan lapisan dekarburisasi sepenuhnya meningkat secara beransur-ansur dengan peningkatan suhu sehingga ketebalan lapisan dekarburisasi sepenuhnya mencapai nilai maksimum, pada masa ini untuk terus menaikkan suhu, kadar pengoksidaan spesimen lebih cepat daripada kadar penyahkarbonan, yang menghalang peningkatan lapisan penyahkarbonan sepenuhnya, mengakibatkan aliran menurun. Dapat dilihat bahawa, dalam julat 675 ~ 950 ℃, nilai ketebalan lapisan dekarburasi sepenuhnya pada 750 ℃ adalah yang terbesar, dan nilai ketebalan lapisan dekarburisasi sepenuhnya pada 850 ℃ adalah yang paling kecil, oleh itu, suhu pemanasan keluli ujian disyorkan untuk 850 ℃.
Rajah.1 Histomorfologi lapisan dekarburasi keluli ujian yang dipegang pada suhu pemanasan berbeza selama 1j
Berbanding dengan lapisan separa dekarburisasi, ketebalan lapisan dekarburisasi sepenuhnya mempunyai kesan negatif yang lebih serius terhadap sifat bahan, ia akan mengurangkan sifat mekanikal bahan, seperti mengurangkan kekuatan, kekerasan, rintangan haus dan had keletihan. , dan lain-lain, dan juga meningkatkan sensitiviti kepada retak, menjejaskan kualiti kimpalan dan sebagainya. Oleh itu, mengawal ketebalan lapisan yang dinyahkarburkan sepenuhnya adalah sangat penting untuk meningkatkan prestasi produk. Rajah 2 menunjukkan lengkung variasi ketebalan lapisan dekarburisasi sepenuhnya dengan suhu, yang menunjukkan variasi ketebalan lapisan dekarburisasi sepenuhnya dengan lebih jelas. Ia boleh dilihat dari rajah bahawa ketebalan lapisan dekarburisasi sepenuhnya hanya kira-kira 34μm pada 700 ℃; dengan suhu meningkat kepada 725 ℃, ketebalan lapisan dekarburisasi sepenuhnya meningkat dengan ketara kepada 86 μm, iaitu lebih daripada dua kali ganda ketebalan lapisan dekarburisasi sepenuhnya pada 700 ℃; apabila suhu dinaikkan kepada 750 ℃, ketebalan lapisan dekarburisasi sepenuhnya Apabila suhu meningkat kepada 750 ℃, ketebalan lapisan dekarburasi sepenuhnya mencapai nilai maksimum 120 μm; apabila suhu terus meningkat, ketebalan lapisan dekarburisasi sepenuhnya mula berkurangan dengan mendadak, kepada 70 μm pada 800 ℃, dan kemudian kepada nilai minimum kira-kira 20μm pada 850 ℃.
Rajah.2 Ketebalan lapisan ternyahkarbur sepenuhnya pada suhu yang berbeza
Kesan penyahkarburan pada prestasi keletihan dalam lenturan putaran
Untuk mengkaji kesan penyahkarbonan pada sifat kelesuan keluli spring, dua kumpulan ujian keletihan lentur putaran telah dijalankan, kumpulan pertama adalah ujian keletihan secara langsung tanpa penyahkarbonan, dan kumpulan kedua adalah ujian keletihan selepas penyahkarbonan pada tekanan yang sama. tahap (810 MPa), dan proses penyahkarbonan diadakan pada 700-850 ℃ selama 1 jam. Kumpulan pertama spesimen ditunjukkan dalam Jadual 2, iaitu hayat lesu keluli spring.
Hayat kelesuan kumpulan pertama spesimen ditunjukkan dalam Jadual 2. Seperti yang dapat dilihat dari Jadual 2, tanpa penyahkarburan, keluli ujian hanya tertakluk kepada 107 kitaran pada 810 MPa, dan tiada patah berlaku; apabila tahap tegasan melebihi 830 MPa, beberapa spesimen mula patah; apabila tahap tegasan melebihi 850 MPa, spesimen keletihan semuanya patah.
Jadual 2 Kehidupan keletihan di bawah tahap tekanan yang berbeza (tanpa penyahkarbonan)
Untuk menentukan had keletihan, kaedah kumpulan digunakan untuk menentukan had keletihan keluli ujian, dan selepas analisis statistik data, had keletihan keluli ujian adalah kira-kira 760 MPa; untuk mencirikan hayat keletihan keluli ujian di bawah tegasan yang berbeza, lengkung SN diplot, seperti yang ditunjukkan dalam Rajah 3. Seperti yang dapat dilihat dari Rajah 3, tahap tegasan yang berbeza sepadan dengan hayat keletihan yang berbeza, apabila hayat keletihan 7 , sepadan dengan bilangan kitaran untuk 107, yang bermaksud bahawa spesimen di bawah keadaan ini adalah melalui keadaan, nilai tegasan sepadan boleh dianggarkan sebagai nilai kekuatan keletihan, iaitu, 760 MPa. Dapat dilihat bahawa keluk S - N penting untuk penentuan hayat lesu bahan mempunyai nilai rujukan yang penting.
Rajah 3 Lengkung SN ujian kelesuan lenturan putar keluli eksperimen
Hayat keletihan kumpulan kedua spesimen ditunjukkan dalam Jadual 3. Seperti yang dapat dilihat dari Jadual 3, selepas keluli ujian dinyahkarburkan pada suhu yang berbeza, bilangan kitaran jelas berkurangan, dan mereka lebih daripada 107, dan semua spesimen keletihan patah, dan hayat keletihan berkurangan. Digabungkan dengan ketebalan lapisan decarburized di atas dengan keluk perubahan suhu boleh dilihat, 750 ℃ ketebalan lapisan decarburized adalah yang terbesar, sepadan dengan nilai terendah hayat keletihan. 850 ℃ ketebalan lapisan dekarburisasi adalah yang paling kecil, sepadan dengan nilai hayat keletihan adalah agak tinggi. Ia boleh dilihat bahawa tingkah laku penyahkarbonan sangat mengurangkan prestasi keletihan bahan, dan semakin tebal lapisan dekarburisasi, semakin rendah hayat keletihan.
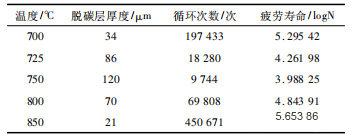
Jadual 3 Hayat kelesuan pada suhu penyahkarbonan berbeza (560 MPa)
Morfologi patah keletihan spesimen telah diperhatikan dengan mengimbas mikroskop elektron, seperti yang ditunjukkan dalam Rajah 4. Rajah 4(a) untuk kawasan punca retak, angka itu boleh dilihat lengkok keletihan yang jelas, mengikut lengkok keletihan untuk mencari punca keletihan, boleh dilihat, sumber retak untuk "mata ikan" kemasukan bukan logam, kemasukan pada mudah untuk menyebabkan kepekatan tekanan, mengakibatkan retak keletihan; Rajah 4(b) bagi morfologi kawasan lanjutan retak, dapat dilihat jalur keletihan yang jelas, adalah taburan seperti sungai, tergolong dalam patah kuasi-dissosiatif, dengan retakan yang mengembang, akhirnya membawa kepada patah. Rajah 4(b) menunjukkan morfologi kawasan pengembangan retak, coretan keletihan yang jelas dapat dilihat, dalam bentuk taburan seperti sungai, yang tergolong dalam patah kuasi-dissosiatif, dan dengan pengembangan retakan yang berterusan, akhirnya membawa kepada patah .
Analisis patah keletihan
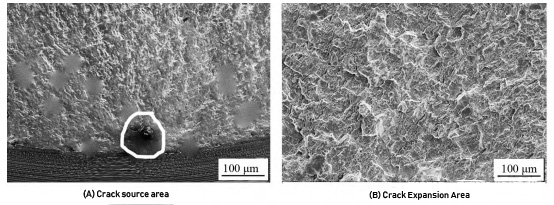
Rajah 4 Morfologi SEM bagi permukaan patah keletihan keluli eksperimen
Untuk menentukan jenis kemasukan dalam Rajah 4, analisis komposisi spektrum tenaga telah dijalankan, dan hasilnya ditunjukkan dalam Rajah 5. Dapat dilihat bahawa kemasukan bukan logam adalah terutamanya kemasukan Al2O3, menunjukkan bahawa kemasukan adalah punca utama keretakan yang disebabkan oleh keretakan inklusi.
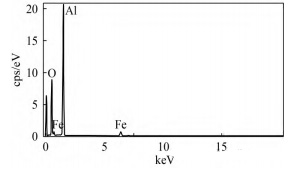
Rajah 5 Spektroskopi Tenaga Kemasukan Bukan Logam
buat kesimpulan
( 1) Kedudukan suhu pemanasan pada 850 ℃ akan meminimumkan ketebalan lapisan dekarburasi untuk mengurangkan kesan ke atas prestasi keletihan.
( 2) Had kelesuan lenturan putaran keluli ujian ialah 760 MPa.
( 3) Keluli ujian retak dalam kemasukan bukan logam, terutamanya campuran Al2O3.
(4) penyahkarbonan secara serius mengurangkan hayat keletihan keluli ujian, semakin tebal lapisan penyahkarbonan, semakin rendah hayat keletihan.
Masa siaran: Jun-21-2024